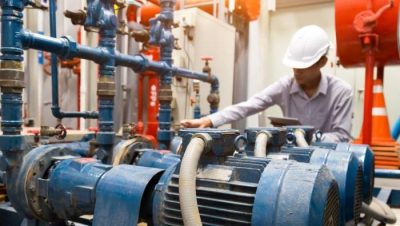
Messungen der Temperatur und Schwingung sind die gebräuchlichste Methode zur Überwachung des Zustands von Pumpen und anderer rotierender Aggregate. Die Überwachung des Motors oder des Lagergehäuses einer Pumpe macht jedoch nur die halbe Wahrheit aus.
Was sind die Hauptgründe für Schwingungen an Pumpen?
Es gibt viele Ursachen für Schwingungen in einer Pumpe. Die häufigsten Ursachen sind Biegekräfte an der Welle, Unwuchten, Fluchtungsfehler und Kontakt zwischen Bauteilen. Diese Probleme können sich alle nachteilig auf die Zuverlässigkeit und den Betrieb rotierender Aggregate auswirken.
Eine Zunahme dieser Vibrationen kann verschiedene Dinge zur Folge haben:
- Übermäßige Wellenbewegung, die eventuell die Dichtung schädigt
- Beschädigungen in den Lagern
- Verändertes Spiel an Buchsen und Verschleißringen
- Teile lockern sich
- Ermüdung und daraus resultierende Beschädigungen
Die Wechselbeziehung zwischen Pumpen – schwingungen mit Prozessdruck und – temperatur
Wenn wir uns eine Pumpe und die Ursachen für einen Pumpenausfall ansehen, müssen wir alle ihre Komponenten genauer betrachten. Es ist wichtig zu beachten, dass Pumpenausfälle nicht immer mit Änderungen der Vibration und der Oberflächentemperatur beginnen. Einige Störungen an Pumpen beginnen mit Druckänderungen – die sich dann in Vibrationen äußern. Schwankungen in den Eigenschaften des Mediums, Änderungen der Drehzahl oder Richtung, Verstopfungen beim Auslass oder beim Ansaugen sowie verschlissene interne Komponenten können zu Änderungen des Pumpendruckes führen.
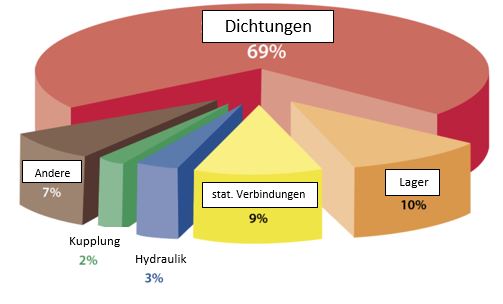
Pumpenstörung – Fall 1: Dichtung
Die Komponente, die bei Pumpen am häufigsten versagt, ist die Dichtung.
Ein Ausfall der Dichtung kann durch mehrere Faktoren verursacht werden, von denen viele im Frühstadium nicht erkannt werden.
Einige der häufigsten Faktoren sind Druckänderungen auf der Saug- und Druckseite der Pumpe, die den Druck und die Temperatur der Dichtungskammer (auch als Stopfbuchse bezeichnet) direkt stören und letztendlich die Gleitringdichtung beeinflussen.
Zum Beispiel: Während des Pumpenbetriebs wird eine Zunahme der Vibration, gefolgt von einer Zunahme der Prozesstemperatur der Dichtungskammer und eines Druckabfalls, festgestellt. Die Ursache ist wahrscheinlich eine Beschränkung auf der Saugseite einer Pumpe.
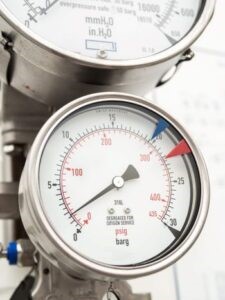
Wenn in diesem Szenario nur die Lagervibration und die Oberflächentemperatur überwacht werden, bleiben Prozessänderungen in der Pumpe unbemerkt. Bei einem Anstieg der Temperatur in der Dichtungskammer und einem Druckabfall kann die Dichtungsvorrichtung (z. B. eine einzelne Gleitringdichtung oder eine doppelte Gleitringdichtung mit einem Puffersystem) trockenlaufähnlichen Bedingungen ausgesetzt sein, was zu einem vorzeitigen Versagen der Dichtung und letztendlich zum Ausfall der Pumpe führt.
Bei einer doppeltwirkenden Gleitringdichtung ( GLRD ) mit Sperrflüssigkeit hilft die Überwachung des Druckes und der Temperatur des Sperrflüssigkeitstanks sowie der Prozessflüssigkeit in der Pumpe dabei, die richtige Druckdifferenz zu bestätigen, die erforderlich ist, um eine ausreichende Schmierung und einen angemessenen Betrieb der Dichtung sicherzustellen. Die Überwachung von Prozessdruck und -temperatur in Kombination mit Vibrationen kann ein klares Verständnis des Pumpenzustandes liefern und dabei helfen, Störungen zu erfassen, um Ausfälle zu vermeiden und die Betriebszeit zu erhöhen.
Pumpenstörung – Fall 2: Lager
Die zweithäufigsten Komponenten, die bei Pumpen ausfallen, sind die Lager.
In der Regel werden Lagerausfälle durch Korrosion, Dichtungsleckage, Unwucht der Ausrüstung, Wellenfehlausrichtung, beschädigtes Laufrad und andere Dinge verursacht. Die Wartung der Lager ist normalerweise vorbeugend. Die Lager werden beim Austausch der Dichtung häufig ausgetauscht, auch wenn diese noch in gutem Zustand sind.
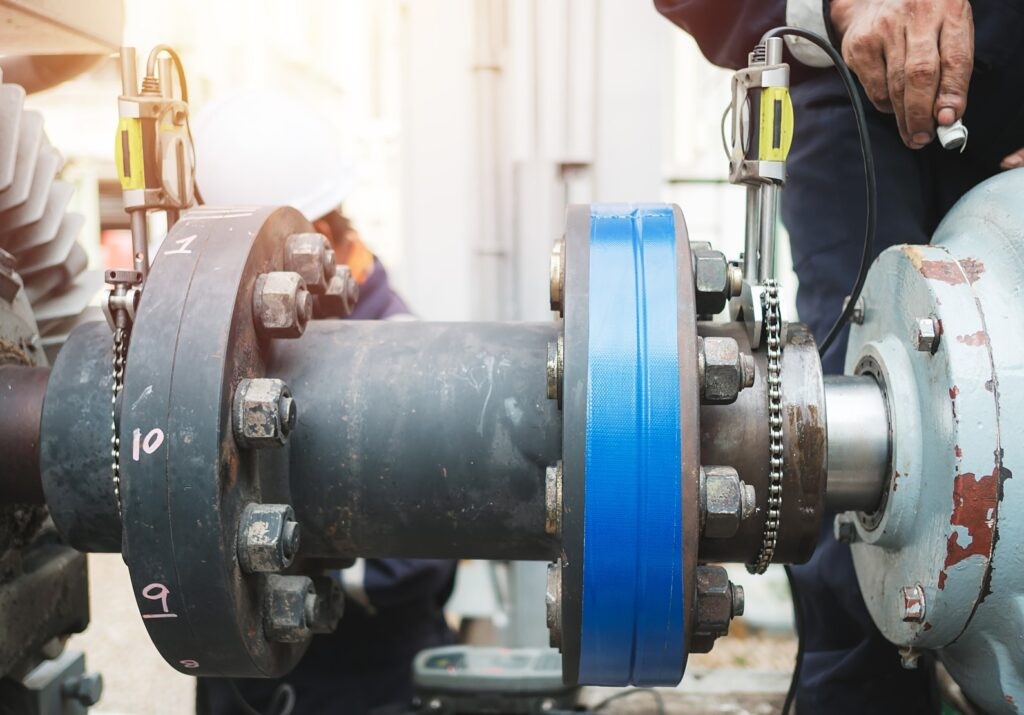
Vollständige Überwachung des Pumpenzustands
Zusammenfassend lässt sich sagen, dass die Überwachung des Druckes, der Temperatur und der Vibrationen des Pumpenprozesses erforderlich ist, um ein vollständiges Bild des tatsächlichen Zustandes einer Pumpe zu erhalten.
Der Chesterton Connect™ – Überwachungssensor, als mobile Anwendung, sowie die Cloud – Analyse, bieten rund um die Uhr eine Sichtbarkeit des Zustands der Aggregate in allen vier Bereichen (Prozessdruck, Prozesstemperatur, Vibration und Oberflächentemperatur). Damit kann man Probleme frühzeitig erkennen und Korrekturen vornehmen. Das erhöht die Zuverlässigkeit und verbessert die Anlagenleistung.
Die folgenden Fallstudien zeigen, wie der Chesterton Connect™ zur Überwachung von Prozessdruck, – temperatur und – vibrationen verwendet wurde, und wichtige Erkenntnisse der Aggregate lieferte.
Fallstudie Nr. 1: Identifizierung von Trockenlaufbedingungen
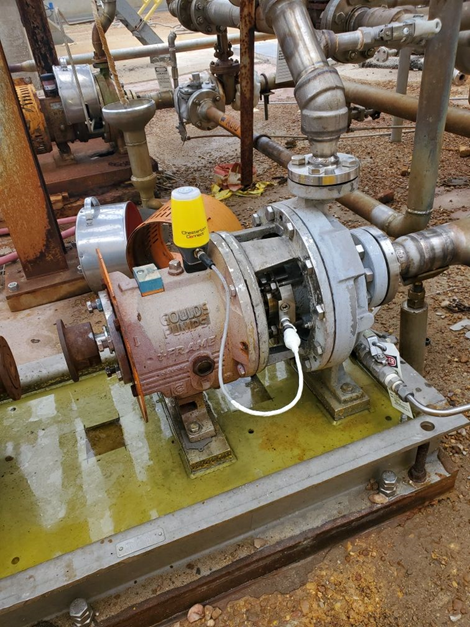
In einer Chemiefabrik kam es bei einer Förderung von Salpetersäure (65% Konzentration) mit Transferpumpen zu einer ungewöhnlich hohen Anzahl von Fehlern bei Gleitringdichtungen. Die mittlere Laufzeit zwischen zwei Reparaturen (MTBR) betrug nur 1,2 Monate.
Ein Techniker überprüfte den Betrieb des Systems sowie die Installation der Gleitringdichtung und stellte keine erkennbaren Probleme fest.
Unser Spezialist empfahl die Installation eines Chesterton Connect™. Innerhalb weniger Tage konnten genug Informationen gesammelt werden, um festzustellen, dass während des Betriebs der Pumpe ein Unterdruck in der Dichtungskammer herrschte. Dieser Unterdruck führte dazu, dass die Gleitringdichtung klassische Trockenlaufsymptome zeigte. Nach Durchführung eines Systemaudits konnte der Kunde ein Ventil zurückdrosseln, um einen ordnungsgemäßen Durchfluss durch die Pumpe sicherzustellen. Die Pumpe und die Gleitringdichtung laufen jetzt ordnungsgemäß und der projizierte MTBR hat sich auf mehr als 24 Monate verbessert. Die potenziellen Kosteneinsparungen für Gleitringdichtungen für diese eine Pumpe betragen mehr als 25.000 €. Die Einsparungen aufgrund reduzierter Wartungs- und Betriebsverbesserungen werden als noch größer eingeschätzt, werden jedoch aktuell noch berechnet.
Fallstudie Nr. 2: Vertikale Turbinen-Druckerhöhungspumpe
Eine zweistufige vertikale Turbinenverstärkerpumpendichtung versagte innerhalb von 2-3 Tagen. Die Dichtung wurde ausgetauscht und versagte innerhalb des gleichen Zeitraums von 2-3 Tagen erneut. Natürlich gab es ein Problem, aber niemand war in der Lage dies zu erkennen. Es war unmöglich, in die Dichtung hineinzusehen, um die Grundursache zu bestimmen.
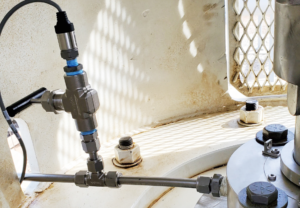
Ein Chesterton Connect – Überwachungssensor wurde installiert, um die Prozessbedingungen zu überwachen, die zu einem vorzeitigen Versagen der Dichtung führen. Mit der Chesterton Connect-App konnte der Benutzer den Prozessdruck (abnehmend) und die Temperatur (steigend) während des Betriebes der Pumpe aufzeichnen.
Aufgrund der Chesterton Connect – Daten wurden kritische Änderungen am Betrieb der Anlage festgestellt und das Problem mit dem Dichtungsausfall behoben.
Originalartikel von Juan Cid